金属加工の種類は何がある?工程や加工法の選び方、注意点など解説
2025年5月8日
現代の製造業において、金属加工は多くの製品や部品製造に欠かせない技術です。
本記事では、金属加工の基本から各種加工方法の特徴、選択のポイントまで幅広く紹介します。製造業に携わる方だけでなく、金属加工に興味のある方も参考にしてください。
金属加工とは
金属加工とはどのようなものか、なぜ必要とされているのか、どのような特徴があるのかを理解することで、各種加工方法の選択や活用方法についての理解が深まります。金属加工の全体像を把握して、効果的な製品製造に役立てましょう。
ここでは金属加工の基本的な定義や目的について解説します。
定義
金属加工とは、金属材料を目的の形状や性質に変える加工作業全般を指します。「工作(手)を加えて形にする」という意味を持ち、人間の手作業から最新のコンピュータ制御による自動加工まで様々な方法があります。
金属加工は大きく「形状を変える加工」と「性質を変える加工」に分類可能です。形状を変える加工には機械加工や塑性加工、鋳造などがあり、性質を変える加工には熱処理や表面処理があります。金属の特性を活かしながら、各種製品の用途に合わせた加工方法が選択されています。
目的
金属加工の主な目的は、原材料の金属に付加価値をつけ、特定の用途に適した製品や部品を製造することです。
金属は強度や耐久性、熱伝導性などの優れた特性を持っているため、様々な機器や構造物に利用されています。加工によって金属の形状を変え、精密な寸法精度を実現したり、熱処理によって硬度や耐摩耗性を向上させたりします。
また表面処理によって耐食性や装飾性を高めることもできます。
金属加工は製品の機能性や安全性、信頼性を確保する上で欠かせない工程です。
金属加工の種類
金属加工には大きく分けて成形加工、除去加工、付加加工、熱処理加工、表面処理加工などがあり、それぞれに特徴や適した用途があります。各加工方法の原理や特性を理解することで、目的に合った最適な加工方法を選択できるようになります。
ここでは様々な金属加工の種類とその特徴について詳しく解説します。
成型加工
成形加工は、金属材料を目的の形状に加工する方法で、材料の塊を製品形状に成形します。代表的な方法には鋳造、鍛造、プレス加工などがあります。
鋳造は溶かした金属を型に流し込んで固める方法で、複雑な形状の製品を作ることが可能です。鍛造は金属を叩いて成形する方法で、強度の高い製品が得られます。プレス加工は金属板を金型で押して成形する方法で、自動車のボディなどに使われています。
鋳造
鋳造は成形加工の代表的な方法で、金属を溶かして鋳型に流し込み、冷却・固化させて目的の形状を作り出す加工法です。
鋳造の歴史は古く、紀元前4000年頃から行われていたとされています。現代では砂型鋳造や金型鋳造、ダイカストなど様々な手法があります。
複雑な形状の製品を一度に成形できる利点がありますが、表面の精度が低いため、多くの場合は鋳造後に切削加工などで仕上げます。エンジン部品や工作機械の土台、モーター部品などに広く使用されており、大量生産に適しています。
プレス加工
プレス加工は、金属板材にプレス機や金型を使って力を加え、切断・曲げ・絞りなどの加工を施す方法です。シャーリングマシンやプレス機、タレットパンチプレスなどの設備を使用し、自動車の外板や家電製品のケースなど幅広い製品に利用されています。
プレス加工の特徴は、同じ品質の製品を短時間で大量に生産できる高い生産性にあります。
一方で、成形できる形状に制限があるというデメリットもあります。バリやシワ、割れといった不良が発生することがありますが、金型設計や機械設定の最適化で対策可能です。
除去加工
除去加工は、金属素材から不要な部分を取り除いて目的の形状を作り出す加工方法です。主に切削加工と研削加工に分けられます。
切削加工では刃物状の工具を使って素材を削り、旋盤やフライス盤、マシニングセンタなどの工作機械が用いられます。研削加工では砥石を使って素材を微細に削り、高い精度の仕上げが可能です。
さらに特殊加工として、放電加工やレーザー加工などもあります。除去加工は精密機器部品や機械部品など、高い精度が求められる製品の製造に適しています。
旋盤加工
旋盤加工は、素材を回転させながら工具(バイト)を当てて削る除去加工の一種です。円筒形の加工や穴あけ、ねじ切りなどに適しており、精密な寸法精度を実現できます。
素材をチャックで固定して回転させ、固定された工具で切削するのが基本的な方法です。従来の汎用旋盤に加え、コンピュータ制御のNC旋盤やCNC旋盤も広く使われています。
旋盤加工では、「ビビり」と呼ばれる振動や「バリ」などの不良が生じることがあるため、適切な回転速度や送り速度の設定が重要です。
研磨加工
研磨加工は、砥石や研磨剤を使って金属表面を削り、滑らかに仕上げる加工方法です。切削加工後の表面を精密に仕上げるための工程として重要で、マイクロメートル単位の精度調整が可能です。砥石研磨、ラッピング研磨、研磨布紙加工など様々な手法があります。
研磨加工は時間あたりの除去量が少なく時間とコストがかかるため、通常は切削加工で形状を作った後、精度が必要な部分のみに施されます。
自動車エンジン部品や工作機械のスライド部など、摩擦や精度が重要な部分の仕上げに使用され、表面粗さや平面度、円筒度などが向上します。
付加加工
付加加工は、金属素材に材料を追加して形状を作る加工方法です。被覆加工と接合加工に大別されます。被覆加工ではペンキ塗装や金メッキなどがあり、接合加工には接着や溶接があります。近年では3Dプリンターを使った金属の積層造形も注目されています。
付加加工の特徴は、複雑な形状や従来の加工方法では困難だった構造の製作が可能な点です。ただし、精度や速度の向上、コスト削減などの課題もあります。
自動車部品や航空機部品、特殊形状の金属製品などの製造に活用されており、今後も技術の発展が期待されています。
はんだ付け
はんだ付けは、はんだと呼ばれる低融点合金を溶かして金属部品を接合する付加加工の一種です。電子機器の基板実装や配管の接合などに広く使われています。
はんだ付けは比較的低温(約200〜350℃)で行えるため、接合する部品へのダメージが少なく、精密な接合が可能です。
はんだには鉛を含む従来のはんだと、環境に配慮した鉛フリーはんだがあります。適切なフラックスを使用して酸化を防ぎ、清潔な接合面を準備することが良好なはんだ付けの鍵です。
電気的な接続と機械的な固定の両方を実現できる利点がありますが、高い強度を要する部分には適さない場合もあります。
溶接
溶接は、金属部品を高温で溶かして一体化させる接合加工の方法です。アーク溶接、TIG溶接、MIG溶接、MAG溶接など様々な種類があり、接合したい金属や求められる強度、精度によって最適な方法が選ばれます。
溶接は金属素材自体と接合材料を溶かして強固に接合できるため、高い強度が必要な構造物や機械部品の製造に欠かせません。
ただし、溶接部に歪みや残留応力が生じる可能性があるため、適切な前処理や後処理、溶接条件の管理が重要です。
熱処理加工
熱処理加工は、金属の内部組織を変化させて機械的性質を向上させる加工方法です。金属を加熱・冷却することで硬度、強度、靭性などの特性を制御します。代表的な全体熱処理には、焼入れ、焼戻し、焼なまし、焼ならしなどがあります。
焼入れは金属を硬くする処理で、焼戻しは硬くなった金属に適度な粘りを持たせる処理です。焼なましは金属を軟らかくして加工性を高め、焼ならしは組織を均質化します。
また表面熱処理では、浸炭や窒化などがあります。自動車や航空機の部品、工具など、強度や耐久性が求められる製品に広く使用されています。
表面処理加工
表面処理加工は、金属の表面に処理を施して耐食性、耐摩耗性、装飾性などを向上させる加工方法です。主な方法には、めっき、研磨、塗装、ショットブラストなどがあります。
表面処理は製品の寿命延長や機能性向上、美観向上などの目的で行われます。金属製品の最終工程として重要な役割を担っており、用途や要求される性能に応じて適切な処理方法が選択されます。
各表面処理方法には特徴があり、コストや効果、環境への影響なども考慮して選ばれます。
めっき
めっきは、金属の表面に別の金属の薄い皮膜を形成する表面処理方法です。錆びにくくする、硬度を上げる、電気の伝導性を高める、装飾性を向上させるなど様々な目的で行われます。
電気めっき、無電解めっき、乾式めっきなど複数の手法があり、金、銀、銅、ニッケル、クロム、亜鉛など多様な金属が皮膜として使用されます。電子部品や自動車部品、家庭用品など幅広い製品に適用されています。
めっきは塗装より耐久性や密着性に優れていますが、処理に時間がかかりコストも高くなる傾向があります。環境への配慮から、有害物質を使用しないめっき技術の開発も進んでいます。
塗装
塗装は、金属表面に塗料を塗布して保護膜を形成する表面処理方法です。防錆効果や装飾性の向上、製品の識別など様々な目的で行われます。塗装には吹き付け塗装、浸漬塗装、電着塗装など多様な方法があり、製品の形状や要求される品質によって選択されます。
塗装はめっきと比べて再塗装が容易で、コストも比較的低いというメリットがあります。一方、めっきほどの耐久性や密着性はないというデメリットもあります。
自動車のボディ、家電製品、建築金物など、多くの金属製品に使用される重要な表面処理です。環境に配慮した水性塗料や粉体塗料の使用も増えています。
金属加工方法の選び方
様々な金属加工方法がある中で、どのように最適な方法を選べばよいのか、多くの製造業の方が悩む問題です。
ここでは金属加工方法を選ぶ際のポイントについて解説します。
目的で選ぶ
金属加工方法は、製品の目的や要求される性能に応じて選択するのが基本です。
高い精度が求められる精密機器部品には切削加工や研削加工が適しています。大量生産が必要な自動車部品などには鋳造やプレス加工が効率的です。
強度や耐久性が重要な部品には鍛造が選ばれることが多く、複雑な形状を実現したい場合は3Dプリンティングや鋳造が考えられます。また、装飾性を重視するならめっきや塗装、耐食性が必要なら表面処理加工が適しています。
製品の用途や機能を明確にし、それを実現するための最適な加工方法を選ぶことが、品質とコストのバランスを取る上で重要です。
金属の種類で選ぶ
金属の種類によって適した加工方法は異なります。
アルミニウムは比較的柔らかく加工しやすいため、切削加工やプレス加工に向いています。鉄鋼は強度があり熱処理効果も高いため、鍛造や熱処理加工が効果的です。
ステンレス鋼は切削抵抗が大きいため、適切な条件での切削加工や特殊加工が必要です。銅や真鍮は熱・電気伝導性に優れ、切削性も良好です。
チタンやインコネルなどの難削材は、特殊な工具や加工条件が必要になります。
金属の機械的特性や熱的特性、化学的特性を理解し、その特性を活かせる加工方法を選ぶことが、効率的で高品質な製品製造につながります。
工具や工機で選ぶ
利用可能な工具や工作機械も加工方法選択の重要な要素です。
高精度な切削加工を行うには、CNCマシニングセンタやNC旋盤などの高性能工作機械が必要です。大型のプレス加工には大きなプレス機が必要ですし、めっきや熱処理は専用の設備が必要です。
自社に既存の設備がある場合は、その設備を活用できる加工方法を選ぶことでコスト削減になります。新たに設備投資をする場合は、生産量や加工精度などを考慮して最適な機械を選定する必要があります。
また、工具の選択も重要で、加工する金属の種類や形状に適した工具を使用することで、加工精度の向上や工具寿命の延長が期待できます。
金属加工時の注意点
効率的で安全な金属加工を実現するためには、工具や工期の適切な選定、金属の特性の理解、安全対策など様々な点に配慮する必要があります。これらの注意点を押さえることで、加工トラブルを減らし、高品質な製品を効率的に製造可能です。
ここでは金属加工を行う際の重要な注意点について解説します。
工具や工期の選定を適切に行う
金属加工において、工具や工期の適切な選定は品質、コスト、納期に直結する重要な要素です。加工する金属の種類や硬度に合わせた工具材質(超硬、ハイス、セラミックなど)を選び、適切な切削条件(回転速度、送り速度、切込み量)を設定することが必要です。
工期については、各工程にかかる時間を正確に見積もり、余裕を持った計画を立てることが重要です。短すぎる工期は品質低下や事故のリスクを高め、長すぎる工期はコスト増加につながります。
また、工具の摩耗状態を定期的に確認し、適切なタイミングで交換することで、加工精度の維持と工具コストの最適化が図れるでしょう。
金属の特徴を理解しておく
金属加工を効率的に行うためには、扱う金属の特性をよく理解しておくことが不可欠です。
例えば、アルミニウムは熱伝導率が高く、切削時に熱が逃げやすいため高速切削が可能ですが、軟らかく粘りがあるため切りくずの排出に注意が必要です。
ステンレス鋼は耐食性に優れていますが、熱伝導率が低く加工硬化しやすいため、適切な切削油と低い切削速度が推奨されます。チタンは比強度が高く軽量ですが、熱伝導率が低く工具との反応性が高いため、特殊な工具と冷却方法が必要です。
各金属の機械的特性、熱的特性、化学的特性を知ることで、加工トラブルを減らし、高品質な製品を効率的に製造できます。
安全性に留意する
金属加工では安全性への配慮が非常に重要です。
高速で回転する工作機械や鋭利な切削工具、高温の溶融金属など、様々な危険要素が存在します。作業者は適切な保護具(安全メガネ、手袋、作業着など)を着用し、機械の安全カバーやインターロックなどの安全装置を必ず使用しましょう。
また、切削油や研磨粉、めっき液などの化学物質による健康被害を防ぐため、適切な換気と保護具の使用が必要です。設備の定期点検や作業者への安全教育も欠かせません。
加工工程全体を通じてリスクアセスメントを行い、危険要因を特定して対策を講じることで、安全で効率的な金属加工環境を実現できます。
まとめ
金属加工は現代のものづくりに不可欠な技術であり、様々な方法があります。成形加工、除去加工、付加加工、熱処理加工、表面処理加工など、それぞれに特徴とメリット・デメリットがあります。製品の用途や要求される性能、金属の種類、生産量などを考慮して最適な加工方法を選ぶことが重要です。
また、加工時には工具や工期の適切な選定、金属特性の理解、安全性への配慮なども忘れてはなりません。技術の進歩により金属加工の方法は日々進化していますが、基本的な原理や注意点を押さえることで、高品質な金属製品を効率的に製造できるでしょう。
コラム監修者
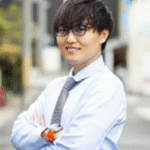
- 代表取締役社長
-
高等学校卒業程度認定試験合格後、関西外国語大学で英米語を専攻し、ニューヨーク州立大学経済学部にも在籍。
その後、同志社大学大学院ビジネス研究科で経営学を深め、現在は京都大学大学院法学研究科で法学を学ぶ。
プライム上場企業で培ったマネジメント力を活かし、経営難だった家業を再建。
一気通貫の機械サービス業の体制構築と品質・納期・コストを革新し、読者のものづくり課題に経営視点で応える。
最新の投稿
- 2025年7月24日アルミ板金加工とは?特徴や難しいといわれる理由、加工ポイントなどを解説
- 2025年7月17日金属の切削加工まとめ|加工の種類や材料、加工ポイントや事例など
- 2025年7月10日樹脂成形基本ガイド|定義や樹脂の種類、加工法など
- 2025年7月3日金型設計とは?業務内容や平均年収、必要スキルなどを解説