金属の切削加工まとめ|加工の種類や材料、加工ポイントや事例など
2025年7月17日
金属の切削加工は、工具を使って金属材料を削る代表的な加工技術です。旋盤やフライス盤、マシニングセンタなどの工作機械を使い、高精度な部品を製造できます。自動車部品から医療機器まで幅広い分野で活用されており、現代の製造業に欠かせない技術です。
本記事では、金属の切削加工の基本的な知識から、加工の種類、使用する材料や機械、メリット・デメリット、加工時のポイント、具体的な事例まで詳しく解説します。
金属の切削加工とは
切削加工について基本的な定義と目的を解説します。金属加工の中でも特に重要な位置を占める切削加工は、さまざまな産業分野で活用されている技術です。
定義
切削加工とは、工具を使って金属などの材料を削り、目的の形状に仕上げる加工方法です。工具または工作物を回転させながら、材料を少しずつ取り除いていきます。
具体的には以下の2つの方式があります。
- 転削:工作物を固定し、工具を回転させる加工法
- 旋削:工作物を回転させ、固定した工具を当てる加工法
鉛筆削りや木材を削るかんなと同じ原理で、金属に対して行う加工と考えると理解しやすいでしょう。現在では工作機械のデジタル化が進み、コンピュータ制御による自動化も実現されています。ただし、機械ごとに特性があるため、オペレータの技術と経験が重要な役割を果たしています。
用途と目的
切削加工は高精度と複雑形状の両立が可能で、以下のような目的で使用されます。
主な用途
- 精密部品の製造
- 試作品の作成
- 多品種小ロット生産
- 複雑な3次元形状の加工
塑性加工や射出成形とは異なり、金型の準備が不要です。そのため、単品から量産まで柔軟に対応でき、設計変更にも迅速に対応できる利点があります。
金属の切削加工の種類
切削加工は大きく3つの種類に分けられます。それぞれ異なる特徴と適用範囲を持っており、加工する部品の形状や要求精度に応じて選択されます。
旋盤加工
旋盤加工は工作物を高速回転させ、固定した刃物を当てて材料を削る加工法です。円筒状の部品製造に向いている加工方法といえます。
加工内容
- 円筒の外周削り
- 内径の穴あけ
- 雄ネジの加工
- テーパー加工
旋盤の種類
- 汎用旋盤:手動で各種加工を行う
- NC旋盤・CNC旋盤:コンピュータプログラムで自動加工
旋盤加工では、ボルトやシャフトなどの回転体部品を効率よく製造できます。特に同一形状の部品を大量生産する場合に威力を発揮する加工法です。
フライス盤加工
フライス盤加工は、固定した工作物に高速回転する刃物を当てて加工する方法です。ブロック状の材料から複雑な形状を削り出すのに適しています。
使用工具
- 正面フライス
- エンドミル
- 溝フライス
- 平フライス
加工内容
- 面の削り出し
- 段や溝の加工
- 複雑な輪郭形状
- ポケット加工
フライス盤の種類
- 汎用フライス盤:工具の制御を手動で行う
- NCフライス盤:工具の制御を自動で行う
- マシニングセンタ:工具交換も自動で実行
フライス盤加工は旋盤加工よりも幅広い形状に対応でき、現代の製造業で最も多用されている加工法の一つです。
穴あけ加工
穴あけ加工は一般的にボール盤を使用し、回転する工具で材料に穴を開ける加工です。単純な穴あけ以外にも、さまざまな関連加工が可能です。
主な加工内容
- 基本的な穴あけ
- リーマによる穴の精度向上
- 中ぐりによる内径拡張
- ネジ切り加工
穴あけ加工は「穴を開けるだけ」と思われがちですが、使用する工具を変えることで多様な加工に対応できます。精度の高い穴や、特殊な形状の穴も製造可能です。
切削加工する材料
切削加工ではさまざまな材料を扱えますが、材料の性質によって加工の難易度やコストが大きく変わります。主要な材料とその特徴を理解することが重要です。
アルミニウム
アルミニウムは切削加工において最も扱いやすい材料の一つです。軽量で加工性に優れているため、幅広い用途で使用されています。
特徴
- 比重が小さい(2.7 g/cm³)
- 加工性に優れている
- 放熱性が高い
- 比較的安価
アルミニウム加工で注意すべきは構成刃先の発生です。熱伝導率が高いものの、加工条件によっては表面が溶着して工具に付着する現象が起こります。
対策
- エアブローによる切り粉除去
- 切削油の大量使用
- 適切な切削条件の設定
ステンレス
ステンレスは耐食性が高く、強度にも優れた材料ですが、切削加工では難削材に分類されます。
特徴
- 耐食性が高い
- 強度が高い(引張強さ:520MPa)
- 耐熱性に優れている
- 加工が困難
加工時の課題
- 熱伝導性が低く工具に熱がこもる
- 工具寿命が短くなる
- 加工硬化を起こしやすい
- 加工時間が長くコストが高い
ステンレス加工では、適切な工具選択と切削条件の設定が不可欠です。特に切削速度と送り速度のバランスが重要になります。
真鍮
真鍮は銅と亜鉛の合金で、柔らかく加工しやすい材料です。複雑な形状への加工に適しており、装飾品や楽器などに使用されます。
特徴
- 展伸性に優れている
- 柔らかい材質
- 放熱性が高い
- 複雑形状に加工しやすい
加工時の注意点
- 溶解温度が低い
- 切り粉が刃先に付着しやすい
- 適切な冷却が必要
油性クーラントによる刃先冷却や、すくい角の大きい超硬工具による高速切削が効果的です。
金属の切削加工に使う機械
切削加工にはさまざまな工作機械が使用されます。それぞれ得意とする加工内容や特徴が異なるため、目的に応じた機械選択が重要です。
マシニングセンタ
マシニングセンタは工具マガジンにさまざまな切削工具を内蔵し、工程順に自動で工具交換しながら加工できる高機能な工作機械です。
特徴
- 自動工具交換機能
- フライス加工、穴あけ、タップなど多様な加工に対応
- 高精度な加工が可能
- 全工程の自動化
軸数による分類
- 3軸加工機:基本的な3方向の直線運動
- 5軸加工機:直線3軸+回転2軸で複雑形状に対応
多品種小ロット生産や試作品製造に威力を発揮します。一度のセットアップで複数の加工工程を連続実行できるため、生産効率が大幅に向上します。
フライス
フライス盤は回転する工具で材料を削る工作機械の基本形です。用途や制御方式によってさまざまなタイプがあります。
種類
- 汎用フライス盤:手動操作による加工
- NCフライス盤:数値制御による自動加工
- 横形・立形フライス盤:主軸の向きによる分類
ブロック状の材料から複雑な形状を削り出すのに適しており、面削り、溝削り、輪郭加工など幅広い加工に対応できます。
旋盤
旋盤は工作物を回転させて加工する工作機械で、円筒状部品の製造に特化しています。
種類
- 汎用旋盤:手動による送り操作と工具交換
- NC旋盤:コンピュータ制御による自動加工
- CNC旋盤:より高度なコンピュータ制御
外径削り、内径削り、ねじ切り、溝入れなどの加工が可能です。特に同一形状の部品を効率よく大量生産する場合に威力を発揮します。
金属を切削加工するメリット
切削加工には他の加工法と比較して多くの利点があります。現代の製造業で広く採用されている理由を具体的に見ていきましょう。
複雑な形に加工できる
切削加工の最大のメリットは、複雑な3次元形状を高精度で製造できることです。
対応可能な形状
- 自由曲面
- アンダーカット形状
- 深い穴や細い溝
- 複雑な内部構造
5軸加工機やマシニングセンタを使用することで、従来の加工法では実現困難な形状も製造可能になります。CAD/CAMソフトウェアとの組み合わせにより、設計データから直接加工プログラムを作成できる点も大きな利点です。
量産に向いている
切削加工は単品から量産まで柔軟に対応できる加工法です。
量産対応の特徴
- NC制御による安定した品質
- 自動化による人件費削減
- 24時間無人運転も可能
- 品質のばらつきが少ない
同一プログラムを使用することで、熟練度に関係なく一定品質の製品を製造できます。また、工具交換や段取り替えの自動化により、生産効率が大幅に向上します。
後加工が少なくすぐに使用できる
切削加工で製造された部品は、多くの場合そのまま使用できる精度と表面品質を持ちます。
利点
- 表面粗さの細かい制御が可能
- 寸法精度が高い
- バリ取りなどの後工程が最小限
- 組立てまでの時間短縮
加工工程の削減により、全体的な製造コストを抑制できます。特に精密部品においては、切削加工後すぐに検査・出荷できる品質レベルを実現できる点が重要です。
金属を切削加工するデメリット
切削加工にはメリットがある一方で、いくつかのデメリットも存在します。これらを理解して適切に対策することが重要です。
ヤケやバリが発生する
切削加工では工具と材料の摩擦により、さまざまな問題が発生する可能性があります。
発生する問題
- ヤケ:摩擦熱による材料表面の変色や性質変化
- バリ:加工部のエッジに発生する突起状の金属片
- 切り粉:加工時に発生する金属屑
対策方法
- 切削油やクーラントの適切な使用
- 切削速度の調整
- 適切な工具選択
- バリ取り工程の追加
バリは使用者や作業者のケガの原因となる可能性があるため、適切な処理が不可欠です。
コストがかかる
切削加工は他の加工法と比較してコストが高くなる傾向があります。
コスト要因
- 材料の無駄が多い(削り取られる部分)
- 加工時間が長い
- 工具の摩耗による交換コスト
- 高価な工作機械の償却費
特に難削材の加工では、工具寿命が短くなり、交換頻度が増加します。また、複雑な形状になるほど加工時間が長くなり、コストが上昇する傾向があります。
適切な加工条件の設定や工具選択により、コストを抑制することが可能です。また、設計段階で加工しやすい形状にすることも重要な対策の一つです。
金属の切削加工のポイント
切削加工を成功させるためには、いくつかの重要なポイントを押さえる必要があります。これらを理解することで、品質向上とコスト削減を同時に実現できます。
切削速度を調節する
切削速度は加工品質と効率に大きく影響する重要な要素です。
速度設定の考慮事項
- 材料の硬さ
- 工具の種類と材質
- 要求される表面粗さ
- 工具寿命とのバランス
速度調整の効果 適切な速度設定により、以下の効果が期待できます:
- 加工時間の短縮
- 工具寿命の延長
- 表面品質の向上
- 生産性の向上
速度を上げすぎると工具の摩耗が激しくなり、逆にコストが増加する場合があります。材料と工具の組み合わせに応じた最適な速度を見つけることが重要です。
熱変形に注意する
切削加工では摩擦により高温の熱が発生するため、熱変形への対策が必要です。
熱による影響
- 加工物の寸法変化
- 表面品質の悪化
- 工具の早期摩耗
- 材料特性の変化
対策方法
- 切削油の使用:摩擦を減らし熱を除去
- 適切な切削条件:発熱を抑える条件設定
- 間欠加工:連続加工を避けて冷却時間を確保
- 効果的な冷却システム:大量の切削油やエア冷却
切りくずを除去する
切削加工で発生する切りくずの適切な処理は、加工品質と安全性の両面で重要です。
切りくず処理の重要性
- 加工精度の維持
- 工具寿命の延長
- 表面品質の向上
- 作業安全性の確保
除去方法
- エアブロー:圧縮空気による除去
- 切削油での洗浄:液体による切りくず流出
- チップコンベア:自動的な切りくず搬出
- 定期的な清掃:手動による除去作業
カーボン加工では粉塵が発生するため、特別な除去システムと安全対策が必要になります。
金属の切削加工事例
切削加工はさまざまな産業分野で活用されています。具体的な事例を通して、その応用範囲の広さを理解しましょう。
自動車部品
自動車産業では、切削加工が多くの部品製造に活用されています。
代表的な部品
- アルミホイール:デザイン性の高い複雑形状
- エンジン部品:シリンダーブロック、ピストン
- ブレーキ部品:ディスクローター、キャリパー
- トランスミッション部品:ギア、シャフト
EV関連部品 電気自動車の普及に伴い、新しい切削加工ニーズが生まれています:
- モーターコア金型:走行用モーター製造用
- バッテリー関連部品:冷却システム部品
- インバーター部品:電力制御用精密部品
医療機器
医療分野では、人体に直接関わる部品のため、特に高い精度と品質が求められます。
医療用部品の例
- 骨固定用ボルト:ステンレスやチタン製
- 人工関節部品:精密な表面仕上げが必要
- 手術器具:複雑な形状と鋭利な刃部
- 歯科用インプラント:チタン合金の精密加工
医療機器では生体適合性の高い材料が使用されるため、難削材の加工技術が重要になります。ステンレスやチタンなどの加工には、特別な工具と技術が必要です。
まとめ
金属の切削加工は、工具を使って材料を削る代表的な加工技術で、旋盤加工、フライス加工、穴あけ加工の3つに大別されます。アルミニウム、ステンレス、真鍮などさまざまな材料に対応でき、マシニングセンタなどの高性能な工作機械により高精度な部品製造が可能です。複雑形状の加工や量産対応などのメリットがある一方で、ヤケやバリの発生、コストの高さなどのデメリットもあります。
コラム監修者
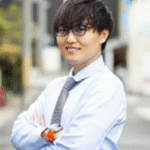
- 代表取締役社長
-
高等学校卒業程度認定試験合格後、関西外国語大学で英米語を専攻し、ニューヨーク州立大学経済学部にも在籍。
その後、同志社大学大学院ビジネス研究科で経営学を深め、現在は京都大学大学院法学研究科で法学を学ぶ。
プライム上場企業で培ったマネジメント力を活かし、経営難だった家業を再建。
一気通貫の機械サービス業の体制構築と品質・納期・コストを革新し、読者のものづくり課題に経営視点で応える。
最新の投稿
- 2025年8月28日ステンレス板金の加工方法は?種類や特徴、注意点をわかりやすく解説
- 2025年8月22日金属加工会社選びで失敗しないための知識|種類・費用・依頼の流れを解説
- 2025年8月14日タングステンの加工方法|特徴や用途、加工の注意点など紹介
- 2025年8月7日圧縮成形とは?加工の特徴やメリット・デメリット、加工方法を解説