レーザーカットする金属加工|加工できる金属やメリット・製品例とは
2025年5月1日
金属加工の世界では、レーザーカット加工が注目を集めています。レーザーの集中したエネルギーを利用して金属を自在に切断・加工できるこの技術は、複雑なデザインの実現や高精度な部品製造を可能にしました。
本記事では、レーザーカット加工の基本から、対応できる金属種類、製品例、メリット・デメリットまで徹底解説します。
金属のレーザーカット加工とは
レーザーカット加工とは、高エネルギーのレーザー光を金属に照射して切断や穴あけなどを行う技術です。従来の機械加工と異なり、非接触で加工できるため仕上がりが美しく、複雑な形状も自由に作れます。特に試作品や少量生産に適しており、金型製作費がかからないため初期コストを抑えられる点が大きな特徴です。
仕組み
レーザー加工の仕組みは、虫眼鏡で太陽光を集めて紙を燃やす原理と似ています。レーザー発振器で生成したレーザー光を反射ミラーと集光レンズで一点に集め、そのエネルギーで金属を溶かしたり蒸発させたりします。
加工時にはアシストガス(酸素、窒素など)が同時に噴射され、溶けた金属を吹き飛ばしたり、光学部品を保護したりします。レーザーの種類や出力、波長によって切断できる金属の種類や厚みが異なり、精密な加工が可能です。
目的
レーザーカット加工の主な目的は、金属部品を高精度かつ効率的に製造することです。
従来の機械加工では難しかった複雑な形状や微細な加工、内角の鋭角な切り出しなどが可能になりました。
また、設計変更があった場合もデータを修正するだけですぐに対応できるため、製品開発のスピードアップや多品種少量生産に適しています。金型を使わないため初期投資を抑えられ、試作品製作から量産まで柔軟な生産体制を構築できます。
レーザーカット加工できる金属の種類
様々な金属素材にレーザーカット加工が適用できることは、製造業において大きな強みです。各種金属によって加工特性が異なるため、目的に合わせた最適な加工方法と素材選びが重要です。
鉄
鉄は最も一般的にレーザーカット加工される金属です。機械部品や建築金物、看板など幅広い用途に使われています。入手しやすく加工しやすいため、様々な板厚の製品製作が可能で、自由な形状に精密に切断できます。
熱延鋼板(SS400)や冷延鋼板、縞鋼板など種類によって特性が異なりますが、高出力のファイバーレーザー加工機を使用すれば最大25mm程度の厚さまで対応可能です。また、切断面が美しく仕上がるため、後処理なしでそのまま使用できるケースも多いです。
銅
銅は通電性に優れた金属で、電気自動車や新幹線などの電気系統に多く使用されています。反射率の高い特性を持つため、レーザー加工は高い技術力と専用機器が必要です。特にファイバーレーザーを使用することで、反射光によるトラブルを防ぎながら高品質な加工が可能です。
高出力のファイバーレーザー加工機を使用すれば、最大10mm程度の板厚まで切断でき、反射を抑えるために出力を適切に調整することで美しい仕上がりを実現できます。銅は単価が高いため失敗が許されない加工といえるでしょう。
アルミニウム
アルミニウムは軽量で軟らかく加工性に優れており、自動車や航空機、建築材料など幅広い分野で使用されています。鉄からの材料変換が進む中、その「軽さ」を生かした用途が増加しています。
レーザー加工には高出力が必要ですが、ファイバーレーザーを使用することで最大25mm程度の板厚まで対応可能です。熱伝導率が高いため切断時の熱影響を考慮する必要がありますが、適切な条件設定により精密に加工できます。特にノートPCのシールドケースなど、薄板で複雑な形状の部品製作に適しています。
チタン
チタンは軽量でありながら高強度という特徴を持ち、自転車やバイク部品、医療機器など特殊用途に使用されています。耐食性にも優れているため、鉄やステンレスからの材料変換も進んでいます。
ファイバーレーザー加工機では約6mm程度の板厚まで対応可能で、難削材であるにもかかわらず精度の高いカットが可能です。チタンをレーザーカットする際は、酸化を防ぐためにアルゴンなどの不活性ガスを使用します。
ステンレス
ステンレスは錆びにくく、耐食性・耐熱性に優れた金属です。厨房用品、食器、医療機器、航空機部品など幅広い用途に使われています。
酸洗材、2B仕上げ、研磨仕上げなど様々な表面処理がされたステンレスに対応可能で、高出力のファイバーレーザー加工機を使えば25mm程度の板厚まで切断できます。
仕上がりが美しく、複雑な形状も精密に加工できるため、デザイン性の高い製品製作に適しています。指先に乗るほど小さな精密部品から大型の建築部材まで、幅広いサイズ対応が可能です。
レーザーカット加工でできる金属製品
レーザーカット加工技術の進化により、様々な金属製品の製造が可能になりました。精密さと柔軟性を兼ね備えたこの加工法は、多種多様な業界で採用されています。
電子機器
電子機器分野では、レーザーカット加工が筐体や内部パーツの製造に活用されています。携帯電話やタブレット、ノートパソコンなどのシールドケースは、電磁波を遮断するために精密な金属パーツが必要です。
レーザーカットなら複雑な形状や微細な穴も高精度で加工でき、デバイスの小型化・軽量化に貢献します。また、基板固定用のブラケットや放熱用のヒートシンクなど、内部部品も効率よく製造できます。電子機器は薄い金属板を使用することが多いため、変形が少なく精密なレーザーカット加工が適していると言えるでしょう。
板ばね
板ばねは産業機器、自動車、航空機、医療機器、AV機器など様々な分野で使用される重要な部品です。金属の弾性を利用した機構部品であり、正確な形状と寸法が求められます。
レーザーカット加工は、金型を使わずに様々な板ばねを製造できるため、試作開発から少量生産まで柔軟に対応できます。また、非接触加工のため材料に余計な応力がかからず、ばねとしての性能を損なわないという利点もあります。
複雑な形状の板ばねも図面データから直接加工できるため、設計自由度が高く、製品開発のスピードアップにつながるでしょう。
ネームプレート
ネームプレートや銘板は、製品に情報を表示するための重要な部品です。レーザーカット加工では、切断と同時に文字やロゴをマーキングできるため、効率的な製造が可能です。
ステンレスやアルミなど様々な金属でシャープな仕上がりの銘板が作れ、会社ロゴや製品情報、シリアル番号などを美しく表現できます。特に少量多品種の製造に適しており、製品ごとに異なる情報を持つ銘板も効率よく生産できます。
また、装飾的な切り抜きを施したデザイン性の高いネームプレートも製作可能です。
医療機器
医療機器分野では、高い精度と清潔さが求められるため、レーザーカット加工の需要が高まっています。外科手術用の精密器具や医療機器のフレーム、歯科用インプラントパーツなど、複雑で小さな金属部品の製造に活用されています。
ステンレスやチタンなどの生体適合性の高い金属を使用し、バリや不純物が発生しにくいレーザーカットは医療用途に適しています。また、製品のトレーサビリティを確保するため、シリアル番号やロット番号などのマーキングも同時に行えるメリットがあります。
金属をレーザーカット加工するメリット
レーザーカット加工は従来の機械加工と比較して、多くのメリットを持っています。特に金属加工において特性を最大限に活かすことで、高品質な製品を効率的に生産できます。
対応できるデザインや形状の幅が広い
レーザーカット加工の最大の強みは、複雑で精密なデザインに対応できる点です。
直径の小さなレーザービームを使用するため、細かい切り込みや複雑な曲線、シャープな角度などを高精度で実現できます。従来の刃物による加工では困難だった細い線や内角の切削も可能です。
また、加工データはコンピューターで作成するため、デザイン変更があってもソフトウェア上で簡単に修正可能です。金型を必要としないので、試作段階でのデザイン検証や改良も迅速に行えます。
工具にかかる負担が少なくメンテナンスしやすい
レーザーカット加工は非接触加工のため、工具の摩耗や消耗がありません。従来の機械加工では刃物が材料に直接触れるため、使用するにつれて摩耗し、定期的な交換やメンテナンスが必要でした。
一方、レーザー加工では光で切断するため、工具交換の手間や費用を大幅に削減できます。また、インクや薬品などの消耗品も必要ないため、一定の条件で安定した加工品質を維持できます。設備のメンテナンスも比較的シンプルで、多くの加工機には自己診断機能が搭載されており、異常を早期に検出できます。
断面がきれいに仕上げやすい
レーザーカット加工では、素材に直接刃が触れないため、切断面にバリやカエリが発生しにくく、仕上がりが美しいという大きなメリットがあります。
従来のプレス加工などでは、切断後にバリ取りなどの後処理が必要でしたが、レーザー加工ではその工程を大幅に削減できます。特にファイバーレーザーを使用した場合、切断面は非常に滑らかで、多くの場合はそのまま使用できるほどの品質が得られます。また、レーザーは局所的に熱を加えるため、素材全体の歪みや変形が少なく、高い精度での加工が可能です
金属をレーザーカット加工するデメリット
レーザーカット加工には多くのメリットがありますが、その特性上いくつかの制約や注意点も存在します。効果的な加工を行うためには、これらのデメリットを理解し適切に対処する必要があります。
加工の危険性が高い
レーザーカット加工は高エネルギーのレーザー光を使用するため、安全面での配慮が不可欠です。
直接目に入ると失明の危険があり、保護眼鏡の着用が必須となります。特に高反射率の金属(アルミニウムや銅など)を加工する際は、レーザー光が予想外の方向に反射し、機器内部や周囲に損傷を与える恐れがあります。
また、加工中に発生する煙やヒュームには有害物質が含まれる可能性があるため、適切な排気システムの設置が必要です。さらに、レーザー加工機は高圧電源を使用するため、感電のリスクもあります。
加工の危険性に対応するため、安全装置の設置や作業者の教育訓練が重要であり、安全基準に沿った作業環境の整備が必要です。
素早い加工ができない
レーザーカット加工は、非接触でピンポイントに加工を行うため、大量生産や高速加工という点ではタレパン加工などの機械加工に劣る面があります。特に厚い金属板の切断では、レーザーの出力を上げても加工速度に限界があります。
無理に速度を上げるとバリが発生し、かえって後処理が必要になるため注意が必要です。
また、レーザー加工では素材を溶かしながら加工するため、熱影響部が生じることがあります。熱の影響により素材特性が変化する場合があるため、精密な部品製作では考慮が必要です。
さらに、レーザー加工機のランニングコストは比較的高く、レーザーガス代やアシストガス代、電気代などのコストがかかるため、大量生産には向かない場合があります。
金属のレーザーカット加工方法
レーザーカット加工には様々な手法があり、用途に応じて最適な方法を選択することで効果的な加工が可能になります。それぞれの加工方法の特徴と適用範囲を理解しましょう。
穴あけ加工
レーザーによる穴あけ加工は、金属板に精密な穴を開ける方法として広く活用されています。従来のドリル加工と異なり、非接触で行えるため材料への負担が少なく、変形やバリの発生を抑えられます。
直径の小さな穴から大きな穴まで対応可能で、特に板厚の薄い金属の穴あけに適しています。
マイクロ穴あけも可能で、電子部品や精密機器に使用される微細な穴(直径0.1mm程度)も高精度で加工可能です。また、一枚の金属板に多数の穴を開ける場合、プログラミングによって効率的に連続加工できるため、パンチングメタルのような多孔板の製作にも適しています。
切断加工
レーザーによる切断加工は、金属板から複雑な形状の部品を切り出す方法として最も一般的に使用されています。高エネルギーのレーザービームで金属を溶融し、アシストガスで溶けた金属を吹き飛ばしながら切断していきます。
切断速度や出力は材質や板厚によって調整され、鉄なら最大25mm、ステンレスも同程度、アルミニウムも25mm程度まで対応可能です。切断面は滑らかで、多くの場合後処理が不要なほど高品質です。
CADデータから直接加工できるため、複雑な形状も正確に再現でき、設計変更にも素早く対応できます。また、材料の固定が簡単で、切断時の応力も少ないため、薄板や細かな部品の切断にも適しています。
マーキング
レーザーマーキングは、金属表面にシリアル番号、ロゴ、バーコードなどを印字する方法です。レーザーの熱による表面変色(アニーリング)を利用するため、耐久性に優れ、摩耗や化学物質にも強い永久的な印字が可能です。
特にステンレスやアルミニウム、チタンなどの金属に適しており、医療機器や自動車部品など、トレーサビリティが重要な製品に広く使用されています。
マーキングの深さや濃さはレーザーパワーや速度を調整することで変更でき、微細な文字や複雑なロゴも鮮明に表現できます。また、曲面や凹凸のある部品にも対応可能で、製品の目立たない場所にも印字できる柔軟性があります。非接触加工のため素材へのダメージが少なく、高精細なマーキングが可能です。
彫刻
レーザー彫刻は、金属表面を深く掘り込んで立体的な表現を行う加工方法です。マーキングよりも深く素材を削り取るため、指で触れて確認できるほどの凹凸が生じます。銘板や装飾品、記念品など、視覚的なインパクトを与える製品に多く使用されています。
彫刻の深さはレーザーの出力や走査回数で調整でき、浅い彫刻から深い彫刻まで幅広く対応可能です。グラデーションや階調表現も可能で、写真やイラストなどを金属表面に再現できます。
特にステンレスや真鍮などの金属に適しており、耐久性の高い表現が求められる場面で活躍します。ファイバーレーザーを使用すれば前処理なしで直接彫刻できますが、CO2レーザーの場合は金属用マーキング剤を塗布する前処理が必要になります。
金属のレーザーカット加工に使われる加工機器
レーザーカット加工を行うには、材料や用途に適した加工機器の選択が重要です。主に使用される2種類のレーザー加工機について、その特徴と適用範囲を説明します。
ファイバーレーザー
ファイバーレーザー加工機は、レーザー媒質として光ファイバーを利用し、細くピンポイントにレーザー光を集中させることができる最新鋭の加工機です。
特に反射率の高い金属(アルミニウムや銅など)の加工に優れており、CO2レーザーでは難しかった素材にも対応できるのが最大の特徴です。高い吸収率と集光性により、高速かつ高精度な加工が可能で、特に薄板金属の切断やマーキングに適しています。
ランニングコストはCO2レーザーよりも低く、レーザーガスが不要で電気効率も良いため、長期運用ではコスト面でのメリットがあります。
機器自体は高価ですが、メンテナンス頻度が少なく、寿命も長いため、導入時には初期コストとランニングコストのバランスを考慮して判断する必要があります。
CO2レーザー
CO2レーザー加工機は、炭酸ガスを媒質としたレーザー光で加工を行う、もっとも一般的なレーザー加工機です。金属だけでなく、木材やアクリル、ゴム、紙など幅広い素材に対応できる汎用性が特徴です。
ファイバーレーザーよりも比較的安価で導入できるため、多くの加工現場で使用されています。金属の中では特に鉄やステンレスの切断に適しており、薄板から中厚板までの加工が可能です。
しかし、アルミニウムや銅などの高反射率金属の加工には不向きで、反射したレーザー光が光学系に損傷を与える恐れがあります。また、レーザーガスの定期的な交換や光学部品のメンテナンスが必要となり、運用コストはファイバーレーザーより高めになる傾向があります。
まとめ
レーザーカット加工は高精度で美しい仕上がりが特徴の金属加工技術で、鉄、ステンレス、アルミニウム、銅、チタンなど多様な素材に対応します。
複雑な形状加工や少量多品種生産に適し、金型不要で初期コストを抑えられます。ただし安全面への配慮や厚い素材への制約もあります。加工機器はファイバーレーザーとCO2レーザーが主流で、製品製造の幅広い分野で活用されています。
用途に合わせた最適な加工方法を選択し、製造効率の向上につなげましょう。
コラム監修者
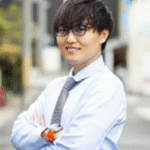
- 代表取締役社長
-
高等学校卒業程度認定試験合格後、関西外国語大学で英米語を専攻し、ニューヨーク州立大学経済学部にも在籍。
その後、同志社大学大学院ビジネス研究科で経営学を深め、現在は京都大学大学院法学研究科で法学を学ぶ。
プライム上場企業で培ったマネジメント力を活かし、経営難だった家業を再建。
一気通貫の機械サービス業の体制構築と品質・納期・コストを革新し、読者のものづくり課題に経営視点で応える。
最新の投稿
- 2025年8月22日金属加工会社選びで失敗しないための知識|種類・費用・依頼の流れを解説
- 2025年8月14日タングステンの加工方法|特徴や用途、加工の注意点など紹介
- 2025年8月7日圧縮成形とは?加工の特徴やメリット・デメリット、加工方法を解説
- 2025年7月24日アルミ板金加工とは?特徴や難しいといわれる理由、加工ポイントなどを解説