真空成形とは?仕組みや射出成型との違い、加工事例などを解説
2025年6月26日
プラスチック製品の製造にはさまざまな手法がありますが、中でも真空成形は比較的簡単な仕組みでありながら、幅広い用途に活用できる技術として注目されています。コストを抑えながら高品質な製品を作ることが可能で、試作品から量産品まで対応できる点が魅力です。
本記事では、真空成形の基本的な仕組みから射出成形との違い、具体的な加工事例まで詳しく解説していきます。
真空成形とは
真空成形は、プラスチック成形技術の中でも比較的わかりやすい仕組みを持つ加工方法の一つです。この技術を理解するためには、まず基本的な定義と仕組みを把握する必要があります。
定義
真空成形とは、熱可塑性プラスチックシートを加熱して軟化させた後、真空によってシートを成形型に密着させて一定の形状に成形する加工方法です。
成形後にプラスチックシートを冷却して固化させ、余分な部分を切断することで製品が完成。シート状の材料を型に合わせて変形させるため、容器や外装カバーなどさまざまな形状の製品を作ることが可能です。
仕組み
真空成形の仕組みは、3つの工程に分かれています。
まず、プラスチックシートをヒーターで加熱し、材料を軟化させる工程から始まります。次に、軟化したシートを成形型の上に置き、型の内部から真空吸引を行うことでシートを型に密着させ、同時に冷却して形状を固定。
最後に、シートが完全に固化した後、型から製品を取り出します。この際、真空吸引によって大気圧との圧力差が生まれ、シートが型の形状に沿って変形する仕組みです。
エアースリップ法やプラグアシスト法など、製品の形状に応じて複数の手法が使い分けられます。
圧空成形との違い
圧空成形は真空成形と似た技術ですが、力の加え方に大きな違いがあります。
真空成形が真空吸引によるマイナスの空気圧を利用するのに対し、圧空成形は圧縮空気によるプラスの空気圧を材料に加えて成形を行う方法です。圧空成形の方が高い圧力で材料を型に密着させられるため、より精密でシャープな形状の製品を作れます。
また、圧空成形は複雑な形状や深い絞り加工に適しており、自動車の内装部品や医療機器のカバーなど、高い精度が求められる製品の製造によく使われています。
射出成形との違い
射出成形は、溶融した樹脂を金型に流し込み、冷却・固化させて成形する方法であり、真空成形とは根本的に仕組みが異なります。
射出成形では、凹型と凸型の両方の金型が必要となるため、型の製作費用が高くなります。一方、真空成形では凸型または凹型のいずれか一方のみで成形が可能なため、型の製作費用を大幅に抑えられます。
また、射出成形は大量生産に適しており、1サイクルの成形時間も短いのが特徴です。これに対して真空成形は、小ロットから中ロットの生産や試作品の製作に向いています。
サイズ面では、真空成形が薄肉で大型の製品を得意とするのに対し、射出成形は厚みのある小型〜中型製品の成形に適しています。
真空成形できる素材の種類とは
真空成形で使用できる素材は熱可塑性樹脂に限定されますが、その中でもさまざまな種類の材料を選択可能です。素材選びは製品の用途や要求される性能によって決まるため、各素材の特性を理解することが重要です。
ここでは代表的な素材である塩ビ系樹脂、ABS樹脂、アクリル樹脂について詳しく見ていきます。
塩ビ系樹脂
塩ビ系樹脂の中でも真空成形によく使用されるのは、アクリル変性高衝撃塩ビ板(カイダックなど)です。
この素材は一般的な塩ビを物性的に改良したもので、非常に高い耐衝撃性を持っています。成形性にも優れており、複雑な形状でも偏肉が発生しにくい点も特徴です。
また、耐薬品性や難燃性といった多くの優れた特性を併せ持つため、産業機器のカバーや医療機器の外装など、厳しい環境下で使用される製品に適しています。
色のバリエーションも豊富で、白、黒、透明などさまざまな色調での成形が可能。さらに、木型を使用することでコストを抑えた成形もできるため、試作品や小ロット品の製作にも重宝されています。
ABS樹脂
ABS樹脂は機械的性質のバランスに優れており、耐衝撃性、加工性、硬度に優れた汎用性の高い素材です。
真空成形においては比較的少ないロットでの生産が可能で、着色や特注サイズでの対応も容易になります。塗装、メッキ、印刷などの加飾性にも優れているため、外観品質が重要視される製品に適しています。
自動車部品、家電製品のカバー、ゲーム機の外装などに幅広く使用されており、表面仕上がりも良好です。また、シボ付きのABSシートを使用することで、質感のある製品を作ることも可能になります。成形時の収縮率も安定しているため、寸法精度が要求される部品の製作にも適しています。
アクリル樹脂
アクリル樹脂(PMMA)は、プラスチックの中でトップクラスの透明性を誇る素材です。
光線透過率はガラスに匹敵し、表面硬度も高いため、照明カバーやディスプレイ用途に多用されています。成形性も比較的良好で、複雑な形状でも美しく仕上がるのが特徴です。耐候性に優れているため屋外での使用にも適しており、看板や建築材料としても活用されています。乳半色や各種着色品も用意されており、用途に応じて選択できます。
ただし、耐衝撃性はやや劣るため、衝撃が加わる可能性がある用途では注意が必要です。
真空成形のメリットとは
真空成形は他の成形方法と比較して多くの利点を持っており、特定の用途において非常に有効な技術です。コスト面、生産効率、形状の自由度など、さまざまな観点から真空成形の優位性を理解することで、適切な場面での活用が可能になります。
ここでは、主なメリットについて詳しく解説します。
コストが安い
真空成形の大きな魅力の一つは、初期費用を大幅に抑えられることです。
成形型が凸型または凹型のどちらか片方のみで済むため、射出成形の型費用の6分の1から10分の1程度まで削減できます。特に試作品や小ロット品の場合、木型などの簡易型を使用することでさらにコストを下げることが可能になります。
また、型製作期間も短縮されるため、開発から製品化までの時間とコストを同時に削減可能です。設備投資についても、真空成形機は射出成形機と比較して安価で済み、メンテナンス費用も抑えられます。
生産効率が良い
真空成形は比較的シンプルな工程で製品を作れるため、生産効率の面でも優れています。1つの成形ラインで型を差し替えることにより、複数の製品を効率的に製造することが可能です。
また、連続成形が可能な製品の場合、ロール状の材料を使用して高速で連続生産を行えます。成形サイクルも安定しており、品質のばらつきを抑えながら安定した生産を継続できます。
24時間稼働にも対応できるため、納期が厳しい案件にも柔軟に対応できる点も大きなメリットといえるでしょう。
成形できる形の幅が広い
真空成形は薄肉から厚肉まで幅広い板厚に対応でき、小型製品から大型製品まで柔軟に製造できます。特に大型で薄肉の製品は、射出成形では実現が困難な場合が多く、真空成形の得意分野といえるでしょう。
また、シルク印刷を施した材料を使用することで、成形と同時に装飾加工を行うことも可能です。エンボス加工やバックプリント加工にも対応できるため、デザイン性の高い製品を作れます。深い絞り加工や複雑な曲線形状にも対応でき、自動車のバンパーから精密機器のカバーまで、さまざまな形状要求に応えらえます。
材料の選択肢も豊富で、透明から不透明、各種色調まで自由に選べる点も魅力の一つです。
真空成形のデメリットとは
真空成形には多くのメリットがある一方で、いくつかの制約や注意点も存在します。これらのデメリットを理解しておくことで、真空成形が適さない場合を判断し、他の成形方法との使い分けを適切に行えます。
主なデメリットについて詳しく見ていきましょう。
成形後の仕上げが必要
真空成形では、成形工程の後に必ずトリミング工程が必要となります。成形時にはシート全体を使用するため、製品部分以外の余分な材料を切断し、形状を整える作業が欠かせません。
この工程によって一定量のスクラップが発生し、さらに、トリミング面の仕上げや穴あけなどの二次加工が必要となるケースも少なくありません。これらの追加作業により、製造時間やコストが増加する可能性があります。
NC加工機を使用すれば精密なトリミングが可能ですが、従来のプレス機では対応できない複雑なカットラインがある場合は、追加の設備投資が求められることもあります。
肉厚の変更ができない
真空成形では、シート状の材料を型に沿って変形させるため、部分的に肉厚を変えることはできません。
成形品の肉厚は使用するシートの厚みによって決まり、製品の各部位で異なる強度が求められる場合でも、柔軟な対応が困難です。特に深い絞り加工を行うと、角部分が薄くなりやすいため、設計段階で十分な検討が必要です。
また、射出成形のようにリブやボスなどの補強構造を一体で成形することはできないため、別途取り付けや溶接などの方法によって補強を行う必要があります。さらに、中空成形のように口の狭い容器形状は基本的に対応できないため、形状に一定の制約があることも理解しておく必要があります。
真空成形の加工手順とは
真空成形の製造工程は、大きく3つのステップに分けられます。各工程の詳細を正しく理解することで、品質の高い製品を安定して製造することが可能です。
ここでは、温度管理や圧力制御など、各工程での重要なポイントを押さえながら、具体的な加工手順について解説していきます。
素材の加熱と可塑化
真空成形の第一工程では、プラスチックシートをヒーターで均一に加熱し、成形に適した軟化状態にします。加熱が不十分だと成形時にシートが破れる可能性があり、過度に加熱すると材料が劣化してしまうため、温度管理は非常に重要です。
また、シート全体を均一に加熱することで、成形時の肉厚分布を均等に保つことが可能です。加熱時間は材料の厚みや種類によって調整し、シートが適度にたわむ状態まで軟化させます。この工程では、材料の予備乾燥が必要な場合もあり、特に吸湿しやすい材料では事前処理が品質に大きく影響します。
成形と冷却
軟化したプラスチックシートを成形型の上に配置し、真空吸引によってシートを型に密着させます。
真空ポンプによって型内部の空気を排出し、大気圧との圧力差を利用してシートを型の形状に沿って変形させます。この際、エアースリップ法では圧縮空気でシートを一度膨らませた後に型を突き上げ、プラグアシスト法では補助型(プラグ)を用いてより精密な成形を行います。
成形と同時に冷却を開始し、シートを型の形状のまま安定させるため、所定の温度まで冷却します。冷却は主に型を通じて行われ、効率を高めるために冷却水路が設けられることもあります。適切な冷却処理により、製品の寸法安定性と表面品質が確保されます。
離型
シートが十分に冷却され、形状が安定した後に型から製品を取り出します。離型時には製品にダメージを与えないよう注意深く作業を行い、必要に応じて離型剤を使用することもあります。
離型後は、製品周辺の余分な材料をトリミングして最終形状に仕上げます。この工程では、NC加工機やプレス機を使用して精密なカットを行い、バリ取りや表面仕上げなどの後処理も実施されます。
品質検査では寸法精度、表面状態、強度などを確認し、必要に応じて追加の加工や修正を行います。最終的に、検査に合格した製品が完成品として出荷。この一連の工程を通じて、高品質な真空成形品が製造されています。
真空成形の加工事例とは
真空成形は幅広い業界で活用されており、その汎用性の高さを示すさまざまな製品が製造されています。実際の加工事例を通じて、真空成形の適用範囲と技術的な特徴を具体的に理解できます。
代表的な分野での加工事例について詳しく見ていきましょう。
医療機器カバー
医療機器分野では、清潔性と機能性を両立させた外装カバーの製造に真空成形が広く使用されています。
カイダックやABS樹脂を材料とした医療機器カバーは、耐薬品性と耐衝撃性に優れており、病院環境での過酷な使用条件に耐えることが可能です。白色やアイボリー色の材料を使用することで、医療現場にふさわしい清潔感のある外観を実現しています。
また、シボ付きの材料を使用することで指紋や汚れが目立ちにくくなり、メンテナンス性も向上します。複雑な機器の形状に合わせた精密な成形が可能で、アンダーカット部分がある形状でも圧空成形技術を併用することで対応できます。
自動車部品
自動車業界では、真空成形による大型部品の製造が盛んに行われています。
バンパーやエアロパーツなどの外装部品では、ABS樹脂やAES樹脂を使用し、軽量化と耐久性を両立させています。特にエアロパーツでは、複雑な曲面形状を美しく再現できる真空成形の特性が活かされており、デザイン性の高い製品が製造されています。また、メッキ加工やカーボン調仕上げなどの表面処理にも対応でき、高級感のある外観を実現できます。
内装部品では、ダッシュボードカバーや天井パネルなど大型で薄肉の部品に真空成形が適用されており、軽量化による燃費向上も可能です。さらに、試作段階から量産まで幅広いロットに対応できるため、新車開発のスピードアップにもつながります。
セルフレジカバー
小売業界で急速に普及しているセルフレジシステムの外装カバーにも、真空成形技術が活用されています。
ROA(PC/ABS)やABS樹脂を使用したカバーは、優れた耐衝撃性と美しい外観を両立させており、多くの人が触れる環境での使用に適しています。
特に券売機やセルフレジでは、操作パネル部分の複雑な形状に対応する必要があり、真空成形の形状自由度の高さが重要な要素です。また、さまざまな色調での成形が可能なため、店舗のブランドイメージに合わせたカスタマイズも容易です。
耐候性にも優れているため、屋外設置の券売機にも対応でき、長期間の使用でも色褪せや劣化が少ない特徴があります。さらに、短納期での対応が可能なため、急速に変化する小売業界のニーズにも柔軟に応えられるといえるでしょう。
まとめ
真空成形は型費用が安く短納期での対応が可能な成形技術で、試作品から量産まで幅広く活用されています。製品の要求仕様に応じて適切に選択すれば効率的な製造を実現できるでしょう。
コラム監修者
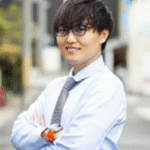
- 代表取締役社長
-
高等学校卒業程度認定試験合格後、関西外国語大学で英米語を専攻し、ニューヨーク州立大学経済学部にも在籍。
その後、同志社大学大学院ビジネス研究科で経営学を深め、現在は京都大学大学院法学研究科で法学を学ぶ。
プライム上場企業で培ったマネジメント力を活かし、経営難だった家業を再建。
一気通貫の機械サービス業の体制構築と品質・納期・コストを革新し、読者のものづくり課題に経営視点で応える。
最新の投稿
- 2025年8月22日金属加工会社選びで失敗しないための知識|種類・費用・依頼の流れを解説
- 2025年8月14日タングステンの加工方法|特徴や用途、加工の注意点など紹介
- 2025年8月7日圧縮成形とは?加工の特徴やメリット・デメリット、加工方法を解説
- 2025年7月24日アルミ板金加工とは?特徴や難しいといわれる理由、加工ポイントなどを解説