難削材とは?チタンやタングステンなどの特徴や加工ポイントなどを解説
2025年5月15日
難削材は航空宇宙産業や医療機器、半導体製造装置など先端産業に欠かせない金属材料です。一般的な金属と比べて加工が困難ですが、優れた特性を持つため特殊な環境で使用されています。
この記事では、チタンやタングステンなどの難削材の特徴や用途、加工方法について詳しく解説します。加工が難しいとされる理由や加工時の注意点も紹介しますので、難削材について理解を深める参考にしてください。
難削材とは
まずは、難削材の定義と基本的な特徴について解説します。
定義
難削材とは切削加工が難しい材料の総称です。
高い硬度や高温での強度維持、化学的安定性などの特性を持ち、通常の加工方法では困難または工具の摩耗が激しいという特徴があります。鉄やアルミニウムと比較して加工時間がかかり、特殊な工具や技術が必要なため、加工コストも高くなります。
しかし、その優れた物理的・化学的特性から、特殊環境や高性能要求がある分野では重要性が年々高まっています。
用途
難削材はその優れた特性により多様な産業分野で活用されています。
航空宇宙産業ではエンジン部品やタービンブレード、医療分野では人工関節やインプラントに使用されます。化学プラントでは耐食性を活かした配管や反応器、原子力発電所では耐熱性と強度を活かした部品として利用されています。
また、自動車産業の高性能エンジン部品や電子機器の特殊部品にも採用されています。
難削材の主な種類と加工用途
ここでは代表的な難削材であるチタン、タングステン、ハステロイ、インコネルについて、それぞれの特徴と主な加工用途を解説します。
チタン
チタンは原子番号22の金属元素で、難削材に分類される代表的な素材です。
比重4.51と鉄の約60%という軽さながら、アルミニウムの約3倍、鉄の約2倍の強度を持ちます。比強度(比重に対する強度)が非常に高く、軽量化が求められる用途に適しています。
また、優れた耐食性を持ち、海水環境でも腐食しにくいという特性があります。純チタンはJIS規格で含有量により1種〜4種に分類され、最も一般的なのは純チタン2種材で、強度と切削性のバランスに優れています。
用途
チタンは軽量で高強度、優れた耐食性という特性から幅広い分野で使用されています。医療分野ではイオン化しにくく金属アレルギーを起こしにくい「生体適合性」を活かし、ペースメーカーやインプラント、人工骨などの医療機器に採用されています。
化学産業では耐食性を活かした配管や反応器に、海洋関連では海水淡水化装置や深海艇の外壁に使用されています。さらにスポーツ用品や日用品分野でも、軽量で丈夫な素材として広く活用されています。
タングステン
タングステン(元素記号W)は原子番号74の金属元素です。
スウェーデン語で「重い石」という意味通り、比重19.30と金(19.32)にほぼ等しく、鉄(7.85)の約2.5倍という高い密度を持ちます。モース硬度9と非常に硬く、金属材料中で最高の融点(約3,600℃)を誇ります。
炭素と結合するとさらに硬度が増し、切削工具材料として重用されています。この高硬度と高融点から難削材として位置づけられています。純タングステンは比較的柔らかいですが、それでもモース硬度9あり、加工には特別な配慮が必要です。
用途
タングステンは高融点と高硬度を活かした用途が多く、切削工具材料が代表的です。高速度鋼や超硬合金の主成分として使用され、その硬さから金属加工に欠かせない存在です。電気抵抗が大きいことから電球のフィラメントに使用され、高温炉の耐熱構造部品としても重宝されています。
高比重を活かして釣り具の錘やバランスウエイト、軍事用途では戦車や装甲車の甲板、砲弾の弾芯などに使われます。放射線遮蔽能力の高さからX線照射機器の遮蔽材としても利用され、医療分野ではカテーテル治療器具にも採用されています。
ハステロイ
ハステロイはニッケルを基とした耐食性に優れた超合金の一種です。強酸や高温環境下での優れた耐性を持ち、化学工業や石油・ガス産業で重要な役割を果たしています。
硬度が高く、加工時には工具の摩耗が激しくなるため、高性能な工具材料の選択や適切な切削速度の設定が必要です。また、熱伝導率が低い特性があり、加工時の熱処理にも細心の注意が必要です。
用途
ハステロイは優れた耐食性を活かした用途が主流です。
化学工業では強酸や強アルカリなど、極端な化学環境下で使用されるプロセス機器や反応器、配管などに使用されます。一般的な金属では腐食する環境でも長期間の使用が可能である点が大きな利点です。
石油・ガス産業では海底掘削装置や高温・高圧環境下での部品に採用されています。
また、塩素製造プラントや廃水処理施設など、腐食性の高い環境にも適しています。材料の耐久性が設備の安全性と長寿命に直結するため、ハステロイの特性が高く評価されています。
インコネル
インコネルもニッケルを基とする耐熱性・耐食性に優れた超合金の一種です。特に高温下での強度維持能力が高く、極限環境での使用に適しています。加工には非常に高い硬度と強度、熱伝導率の低さが課題となり、通常の鋼材よりも高い工具耐久性と冷却方法が必要です。また、作業硬化しやすいという特性があり、加工時には低い切削速度が推奨されることが多いです。
用途
インコネルは優れた高温特性を活かした用途が中心です。航空宇宙産業では高温環境下で使用されるジェットエンジンのタービンブレードや排気システムに採用されています。運用中に極度の高温にさらされるため、インコネルの高温強度が重要な役割を果たします。
エネルギー産業では原子力発電所の核燃料棒や高温高圧を扱う発電所部品に使用されています。化学工業では高温かつ腐食性のある環境の反応器や熱交換器、自動車産業では高性能エンジンの排気システムなどに利用されています。
難削材の加工が難しい理由
難削材の加工が難しい理由はいくつかあります。
まず、熱伝導率の低さが大きな要因です。例えばチタンの場合、加工時の熱が逃げにくく、切削点に熱が集中するため、工具の摩耗が早くなります。
また、金属活性が高い材料が多く、加工中に工具と化学反応を起こしやすいという特性もあります。チタンはヤング率が小さいため、加工時に変形しやすく、特に薄い部品では振動(ビビリ)が発生して精度が低下することがあります。
難削材の加工には特殊な工具や加工条件、冷却方法などが必要となり、専門的な知識と経験が求められます。
難削材を加工するメリット
ここでは難削材を加工する際のメリットについて解説します。軽量性や高強度、耐熱性など、難削材ならではの特性がどのような価値をもたらすのか、産業応用の観点から紹介します。
比較的軽量
チタンのような難削材は、その軽量性が大きなメリットです。
チタンはステンレスの約2/3の重量しかなく、加工や運搬の手間やコストを削減します。金属製装置や機器は大きくなるほど重量が問題ですが、チタンを使用することで部品を軽量化できます。特に高層階への設置時には、その軽さが設置の可否を左右することもあります。
アルミニウムより比重は高いものの、強度や耐食性では優れているため、同じ強度を得るための材料量が少なくて済み、結果として製品全体の軽量化につながります。航空宇宙産業や医療機器、スポーツ用品など、軽量性が重要視される分野で重宝されています。
高い耐久性や強度
耐久性と強度も重要なメリットです。一般的な金属よりもはるかに高い強度を持ち、極端な圧力や衝撃がかかる環境でも破損や変形が少なく、長期間性能を維持できます。
チタンは鉄の約2倍、アルミニウムの約3倍の強度を持ち、変形しても元の形状に戻る特性があります。また、多くの難削材は高温下でも強度や硬度が落ちにくい特性を持っています。
タングステンの融点は約3,600℃と金属材料中最高で、インコネルやハステロイも高温環境での強度維持能力に優れ、エンジン部品やタービンなどの高温環境用途に適しています。さらに化学的に安定しており、腐食性環境でも劣化が少ないため、化学工業や海洋設備にも利用されています。
加工時の安全性
チタンは「生体適合性」という重要な安全特性を持っています。安定した物質でイオン化しにくく、イオン溶出の危険性が少ないため金属アレルギーを起こしにくいという利点があります。
また毒性もないため人体に安全で、医療分野での使用に適しています。チタンの酸化チタン層は抗菌効果も持ち、食器などの用途にも適しています。
加工時には適切な冷却が必要ですが、他の難削材と比べて有害物質発生リスクが低いのも特徴です。インコネルやハステロイのニッケル基合金も、適切な加工条件下では安全に取り扱えます。
難削材の加工方法
ここでは難削材の主要な加工方法について解説します。切断、切削、曲げ、溶接、熱処理など、それぞれの加工技術の特徴と適用方法について紹介します。
切断加工
難削材の切断には主に三つの方法があります。
レーザー加工は集中したレーザー光で材料を溶かして切断し、加熱範囲が小さいため変形が少なく、バリも生じにくいという利点があります。シャーリング加工は刃による切断で、切断速度が速く大量加工に適しています。
ワイヤーカット加工は材料と電極間に電圧をかけて放電を起こし、熱で材料を溶かす方法で、高精度・大量加工に向いています。
チタンやインコネルの切断には硬度や熱伝導率の低さから特に注意が必要で、レーザー出力や送り速度の調整が重要です。タングステンなど非常に硬い材料にはダイヤモンドワイヤーが使用されることもあります。
切削加工
難削材の切削は主にマシニングセンタ、フライス盤、ドリル加工などで行われます。
マシニングセンタは自動工具交換ができ複雑形状の加工に適し、フライス盤は回転刃物で素材を削り小ロット多品種生産に向いています。ドリル加工ではステップフィードやオイルホール付きドリルを使用し、切削熱の蓄積や屑の固着を防止します。
難削材切削では工具摩耗が課題で、チタンなどは熱伝導率が低く加工熱が逃げにくいため工具負担が大きくなります。タングステンやハステロイなど硬い材料には特殊工具や加工条件が必要で、インコネルは作業硬化しやすいため一度の切削で必要深さまで加工することが重要です。
曲げ加工
チタンの曲げ加工には「プレス加工」「密着曲げ」「ベンダー曲げ」などがあります。チタンは弾性が強く「スプリングバック」を起こしやすい特性があります。
これは曲げ加工後に荷重を除くと弾性回復で形状が戻る現象で、チタンでは特に難易度が高いとされています。
曲げ加工時には材料特性に合わせ圧力や角度などを細かく調整する必要があり、寸法や厚みの考慮も重要です。特に厚いチタン板は4mm以上でクラック発生の可能性が高く困難とされますが、特殊熱処理でクラックを抑制できる場合もあります。
難削材の曲げ加工には材料特性の理解と適切な加工条件設定が不可欠で、熱処理や温度管理など専門技術が求められます。
溶接加工
チタンの溶接は難削材加工の中でも最も難しいとされています。その理由は溶接部分が大気に触れると反応し「脆化現象」を起こしやすいためです。
脆化現象とは金属が展延性や靱性を失い脆くなる現象で、チタンは高活性で水や酸素と反応しやすいため特別な注意が必要です。一般的なチタン溶接法はTIG溶接で、溶接中のチタンをシールドガスで包み空気接触を防ぎ脆化や酸化を防止します。
その他MIG溶接、電子ビーム溶接、プラズマ溶接、レーザー溶接などがあります。チタンと他金属の溶接は「金属間化合物」生成のため基本的に不可能です。インコネルやハステロイなど超合金の溶接にも同様の注意が必要で、適切なシールドガスと冷却管理が重要となります。
熱処理加工
難削材の熱処理は材料特性の最適化と加工性改善に重要です。チタン合金では焼鈍(アニーリング)が加工性向上のために行われます。これは材料を700-785℃程度まで加熱し保持後、空冷する処理で、内部応力減少と硬度低下により加工性が向上します。また溶体化処理と時効処理の組み合わせで強度・硬度向上も可能です。
ニッケルベース超合金(ハステロイ、インコネル)の熱処理も溶体化処理と時効処理が主流で、溶体化では高温保持後急冷して合金元素を均一分散させ、時効処理は低温保持後徐冷して硬度・強度を向上させます。
難削材の加工における課題と注意点
ここでは難削材加工に伴う課題と注意点について解説します。コスト面での課題や特殊技術の必要性、工具寿命の問題など、難削材加工特有の問題点を理解し、適切な対策を講じることで、より効率的な加工が可能です。
加工にコストがかかりやすい
難削材加工は一般材料と比べ高コストになりがちです。
難削材は加工速度が遅くなりがちで加工時間が長くなるため、労働コストや設備稼働コストが増加します。さらに材料自体のコストも一般鋼材より高価です。特にタングステンやインコネルなどは入手困難や高価格の場合があります。
加工コストを押し上げていますが、難削材の優れた特性が必要な用途ではコスト以上のメリットがあるため需要は継続しています。
特殊な加工技術を要する
難削材加工には通常の技術では対応できない特殊技術や知識が必要です。高度な技術トレーニングや専門知識が求められ、生産体制構築も難しくなります。
チタン加工では低熱伝導率と高反応性に対処するため特別な冷却方法や切削条件が必要です。熱蓄積は工具摩耗を早めるだけでなく、チタンが酸素や窒素と反応して表面硬化層を形成し加工をさらに困難にします。
タングステンやハステロイなど硬質材料ではダイヤモンド工具や特殊セラミック工具が必要で、インコネルは作業硬化しやすいため一度の切削で必要深さまで加工する技術が求められます。また振動(ビビリ)対策として特別な治具や加工パラメータ調整も必要です。溶接でも大気反応による脆化防止のため特殊シールドガス環境での技術が必要です。
工具や工機の交換を行う
難削材加工では工具摩耗が極めて早く、頻繁な工具交換が必要になります。
チタン加工では熱伝導率の低さから切削点に熱が集中し工具摩耗が早まります。また工具との接触面で凝着しやすく、これも寿命を短くします。タングステンやハステロイなど硬質材料加工では工具負荷がさらに大きくなるため、適切な工具材質選択や切削条件最適化が重要です。
超硬工具やセラミック、CBNなどの高硬度工具材料使用が一般的で、適切な切削油剤や低速高送りの加工条件採用など工具寿命延長の工夫も必要です。
まとめ
本記事では難削材の特徴と加工方法について解説しました。チタンやタングステンなどの難削材は加工が難しい反面、優れた特性から多くの産業分野で重要な役割を果たしています。
これらの材料を適切に加工するためには、材料特性の理解と専門的な加工技術が不可欠です。様々な課題がありながらも、技術の進歩によって難削材の活用範囲は今後も拡大していくことでしょう。
コラム監修者
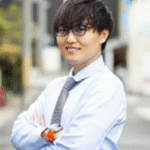
- 代表取締役社長
-
高等学校卒業程度認定試験合格後、関西外国語大学で英米語を専攻し、ニューヨーク州立大学経済学部にも在籍。
その後、同志社大学大学院ビジネス研究科で経営学を深め、現在は京都大学大学院法学研究科で法学を学ぶ。
プライム上場企業で培ったマネジメント力を活かし、経営難だった家業を再建。
一気通貫の機械サービス業の体制構築と品質・納期・コストを革新し、読者のものづくり課題に経営視点で応える。
最新の投稿
- 2025年8月22日金属加工会社選びで失敗しないための知識|種類・費用・依頼の流れを解説
- 2025年8月14日タングステンの加工方法|特徴や用途、加工の注意点など紹介
- 2025年8月7日圧縮成形とは?加工の特徴やメリット・デメリット、加工方法を解説
- 2025年7月24日アルミ板金加工とは?特徴や難しいといわれる理由、加工ポイントなどを解説